Leading-edge brewing and baking
STAMAG Stadlauer Malzfabrik GesmbH (STAMAG), based in Vienna’s 22nd district, is one of Austria’s leading producers of high-quality malt and baking ingredients. As Austria’s largest malting plant, STAMAG supplies both manufacturers of world-famous brands and large breweries as well as craft brewers with base and specialty malts, processing around 260,000 tons of grain per year.
True to the motto “Committed to good tradition, dedicated to real progress”, the company not only sells more than 400 products, but is also constantly investing in the modernization and further development of production. With the help of Siemens technology, a high-tech plant for the production of baking ingredients and currently a new, highly automated malting plant have been realized.
Working together to achieve success
“The former germination boxes got a bit long in the tooth,” confirms Achim Hanninger, Technical Managing Director at STAMAG, and adds: “Furthermore, a cost-intensive refurbishment of the existing system would not have resulted in any improvement in specific energy consumption.” This is why, STAMAG decided to demolish the old plant and build a new one on the resulting open space. Swiss grains & food specialist Bühler was commissioned to design and build the new malthouse. SISTAR – the Siemens process control system for the automation of food processing plants – was chosen for the process control system because of the cooperation between Siemens and its partner and system integrator Mitterhofer Automatisierungstechnik.
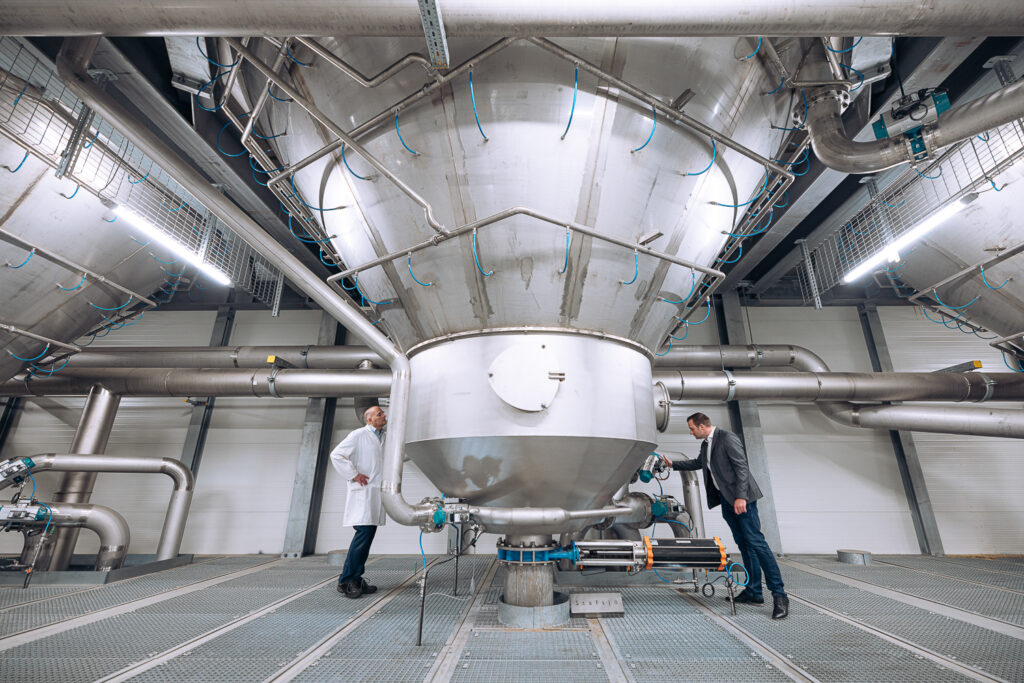
State-of-the-art facilities in the new malthouse
In addition to the SISTAR software licenses, Siemens offered nine S7-1500 programmable logic controllers (PLCs), four clients for the existing servers, the compact SIMATIC ET 200SP IO system, SITOP power supplies and SCALANCE industrial network components, engineering and commissioning as well as planning and delivery of the control cabinets. The project partner Mitterhofer Automatisierungstechnik contributed a significant part of the required programming effort.
More automation for greater precision and quality
The trial operation was completed at the beginning of March 2024. “All elements of the malting plant – conveyor belts, flaps and motors – are controlled via the software and hardware PLCs,” says Andreas Hermann, Sales Specialist Food&Beverage at Siemens. According to the Sales Specialist, the high degree of automation, in combination with the sensors connected to the control units, leads to even more precise data. For example, the speeds of the drives or properties of the product, such as humidity, would be displayed and recorded. In addition, the targeted use of automation technology provides further benefits: “Increasing the degree of automation while reducing the amount of employees required leads to more accurate, precisely reproducible results,” summarizes Hermann.
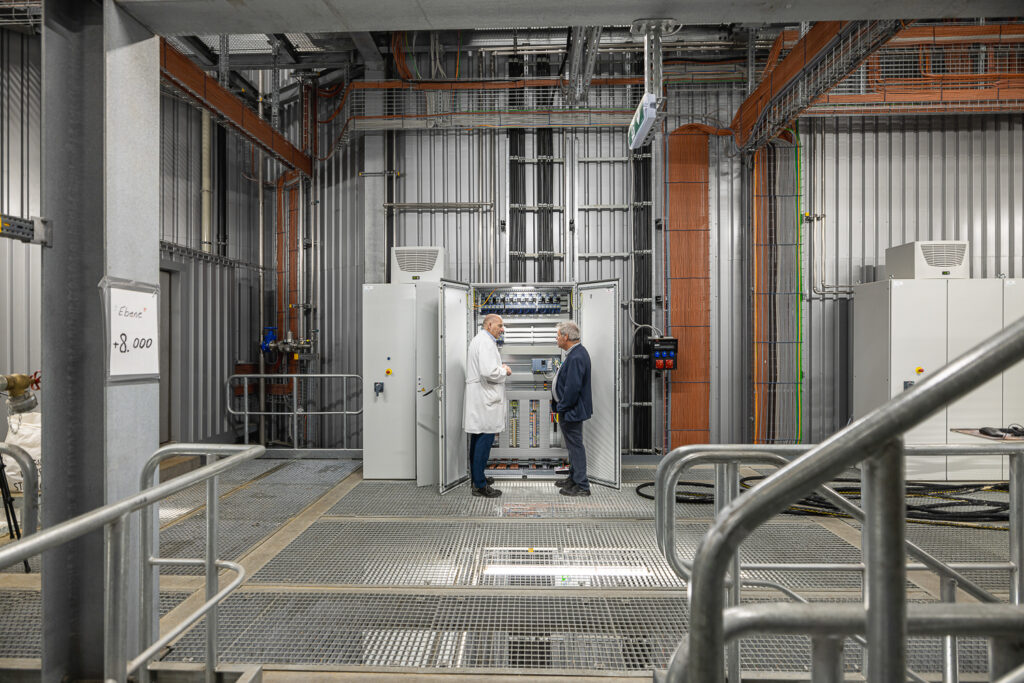
State-of-the-art technology inside the company
Thomas Felkel, Siemens’ Sales Specialist for SISTAR highlights the compatibility between different SISTAR versions, the integrated recipe system and the replay mode as additional STAMAG-relevant features: “This allows previous processes to be ‘replayed’, similar to the eponymous function in the video recorder, for example for analysis or optimization purposes.” Precise and comprehensive batch traceability based on batch numbers plays a crucial role in the food industry in particular: “SISTAR can also be used to create detailed batch reports and step-by-step logs for the legally required traceability of all batches.”
Finger on the process
For Achim Hanninger, SISTAR meets the key requirements of his malting business: “On the one hand, the clear and unambiguous visualization ensures that both skilled and semi-skilled employees interpret the displayed processes correctly. On the other hand, we are meeting our claim of writing down as many parameters as possible in order to be able to understand all occasions — from curves to alarms and step chains.” Also important for Hanninger are the free protocols, the commercial malthouse is using to set up specific scanning, such as batch-specific scanning of various parameters, such as quantities and temperatures, followed by their recording and evaluation. SISTAR also supports the advancing digitalization of the company on the hardware side: “With the SISTAR licenses, we are moving away from PCs with operating systems that are characterized by a limited update and support horizon. Instead, we rely on virtual machines or terminals with server access.”
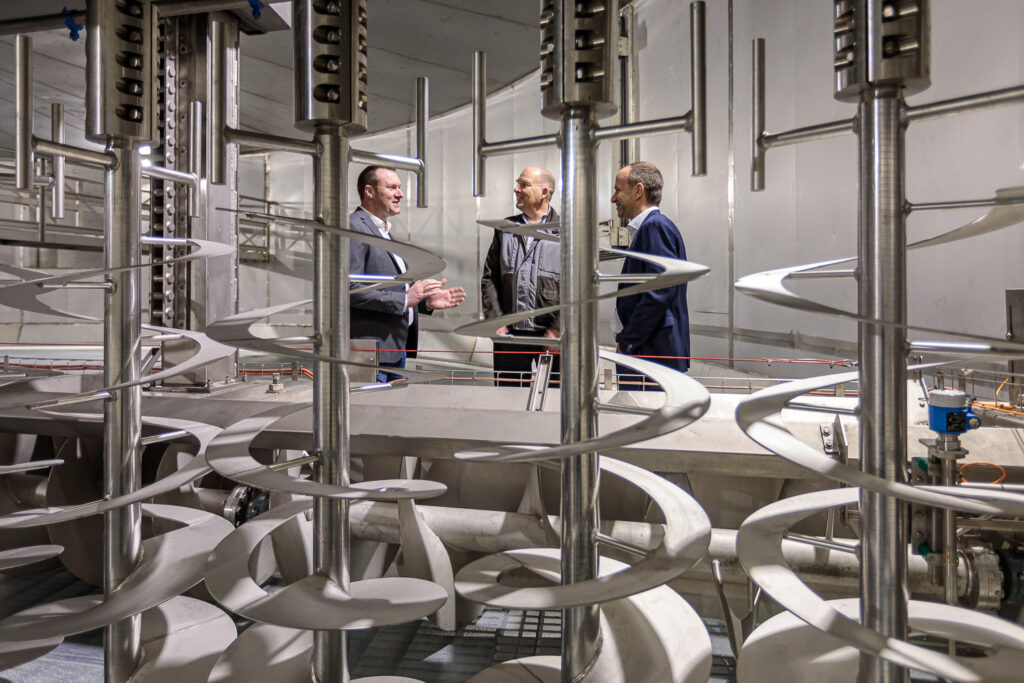
Efficient production through cooperation with Siemens – from left: Andreas Hermann (Siemens), Achim Hanninger, Technical Managing Director at STAMAG, and Thomas Felkel (Siemens)
The standard software leaves nothing to be desired in terms of scalability. As a scalable solution, it can continue to grow with STAMAG’s success and guarantee highly automated, efficient and resource-saving production of quality malts in the future.